Household Tips: Reviving a Dead Laser Cutter.
Not long ago, I happened to come across a very cheap and heavily used CO2 Laser Cutting Machine, made by Full Spectrum Inc. About 1K USD, including curbside delivery from across the continent. I also bought the traditional water chiller, air compressor, exhaust manifolds, etc:
The junk seller promised an intact tube, and indeed there was:
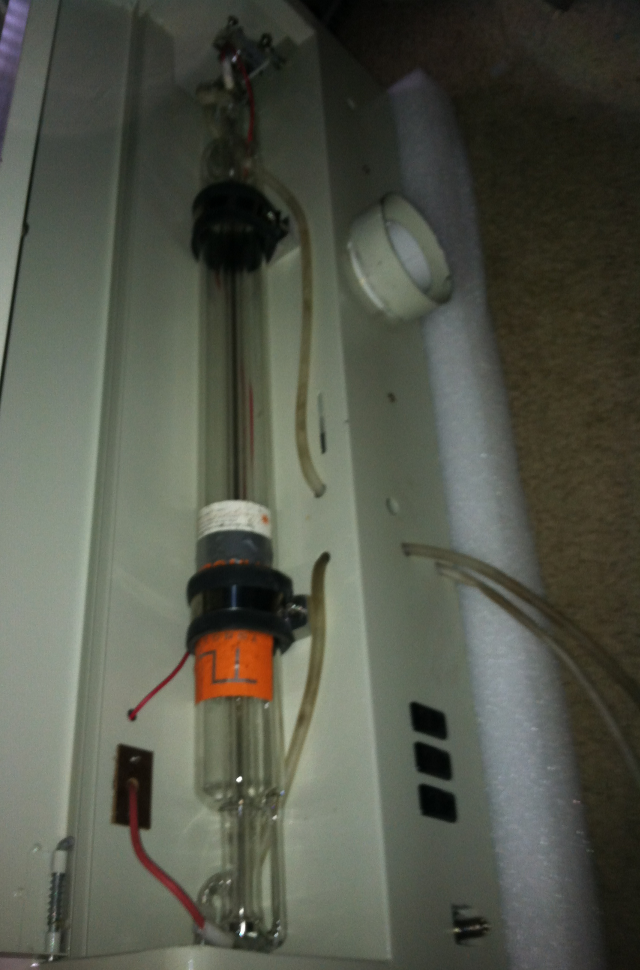
Tube. CO2, Sealed, ~25kV operating voltage.
Naturally, "the miser pays twice." The poor thing released its magic smoke five minutes into the first test run. The laser would still turn on if triggered manually, but the machine had become: an expensive electric drill! The culprit? X-axis stepper motor driver (Allegro Microsystems A3983) seen below:
I then contacted the manufacturer: who demanded a steep "transfer fee" before they would even discuss the sale of a spare. And so, we resort to Chinese methods. The recipe, should you, my dear reader, find yourself in a similar situation:
- Obtain new chip. I found, rather surprisingly, that the A3983 could only be had on eBay, from a Chinese vendor.
- Remove Stepper Motor Driver Board.
- Heat Dead Chip to around 280C with Hot Air Tool.
- Carefully lift Dead Chip off the board with Vacuum Tweezer (or, lacking the latter, a sharp set of ordinary tweezers.)
- Allow board to cool.
- Scrub board with ordinary flux remover. Allow board to dry.
- Coat the pads in solder. Especially the large thermal pad found underneath Stepper Motor Drivers like this one.
- Place new chip on the pads; secure in place with Kapton tape.
- Solder opposite corners, securing the chip. You can now remove the tape.
- Solder remaining pads.
- Remove all unwanted "bridges," with the possible exception of those found on pads that are already connected together on the PCB.
- Heat the area to ~280C using Hot Air Tool to reflow solder over thermal pad.
- Allow unit to cool; re-install in machine.
- "Do Not Look Into Laser With Remaining Good Eye."
Result: a working tool again! The motors buzz merrily, the laser cuts.
There was one remaining write-off: the USB to Parallel dongle (made by Full Spectrum) which plugged into the above controller. It breathes no more, merely heating a bit when plugged into a USB port. I blame its malfunction for the death of the stepper driver, though I lack positive proof. And this weird MS-Windows-only gadget is no great loss: turns out, the purely parallel-port motor board runs perfectly well with LinuxCNC. The end.
Now to add heat sinks (~$0.50 each):
Looks like a nasty short between pins 8&9 slew the original driver chip. Perhaps there was a subtle short? Or one of those tin whiskers? Was this assembled with lead-free solder originally?
http://nepp.nasa.gov/WHISKER/background/index.htm
Dear Dave,
The original solder melted readily near ~280C. So almost certainly: leaded.
Yours,
-Stanislav
Dear Stanislav,
In retrospect the leaded-ness of the solder was obvious from your narrative. Also, I doubt that a whisker would be able to conduct sufficient current to vaporize IC leads before vaporizing itself.
Surprised FS Laser wouldnt at least warranty the part...especially after just turning it on? ?
Dear Ben,
FS Inc. appears to be one of those outfits that doesn't give a rat's arse about your unit if you didn't buy it directly from their catalogue, at their 'golden toilet' price. It is what it is. Keep this in mind when purchasing a second-hand machine of this type.
Yours,
-Stanislav
Hey... don't get it quiet “the miser pays twice.” .. How is this used as twice?